Mantenimiento Productivo Total: La guía definitiva para mejorar tu producción y reducir costos
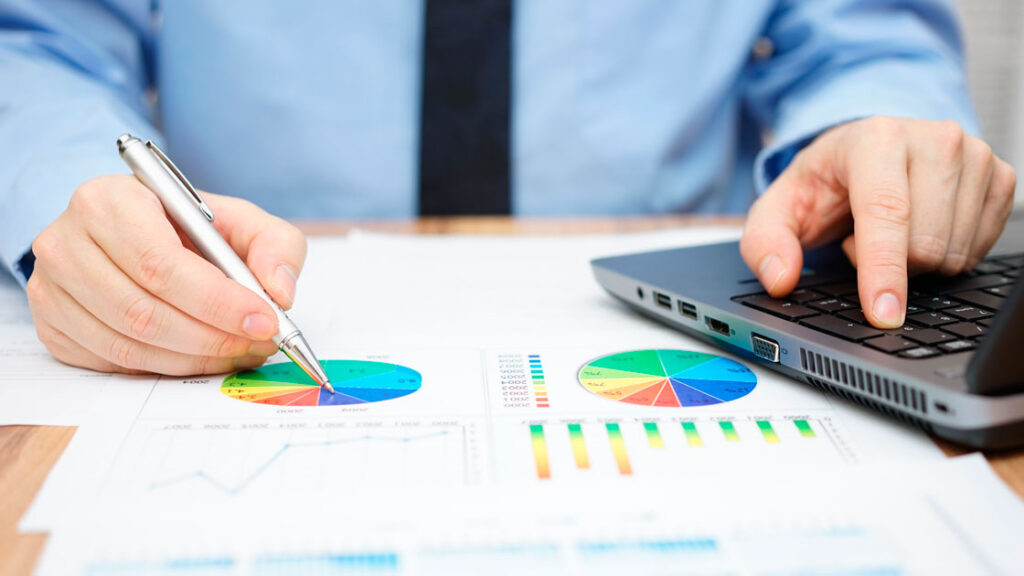
El Mantenimiento Productivo Total, también conocido como TPM por sus siglas en inglés (Total Productive Maintenance), es una metodología de gestión que busca mejorar la eficiencia y efectividad de los procesos de producción de una empresa. Fue desarrollado en Japón a partir de la década de 1960 y ha sido implementado con éxito en numerosas organizaciones alrededor del mundo.
En este artículo te brindaremos una guía completa sobre el Mantenimiento Productivo Total, donde aprenderás qué es, cuáles son sus principios fundamentales, cómo se implementa en una empresa y cuáles son los beneficios que puede brindar. Además, te proporcionaremos consejos prácticos para llevar a cabo una exitosa implementación y lograr así una mejora sostenida en la producción y una reducción significativa de costos.
- ¿Qué es el Mantenimiento Productivo Total (TPM) y por qué es importante para mi empresa?
- Cuáles son los 8 pilares fundamentales del TPM y cómo puedo implementarlos en mis operaciones
- Cómo identificar y eliminar las principales fuentes de pérdida de eficiencia en mi proceso de producción
- Cuál es el papel de la gestión del mantenimiento en el TPM y cómo puedo mejorarla en mi empresa
- Qué herramientas y técnicas puedo utilizar para optimizar el tiempo de actividad de mis activos y reducir los tiempos de paro no planificados
- Cómo realizar un análisis de la eficacia global del equipo (OEE) y utilizarlo como indicador clave de rendimiento en el TPM
- Cuáles son las mejores prácticas para establecer rutinas de mantenimiento preventivo y predictivo en el marco del TPM
- Cómo formar y capacitar a mi equipo de trabajo para que esté alineado con los principios y objetivos del TPM
- Qué beneficios puedo obtener al implementar el TPM en mi empresa y cómo puedo medir su impacto en la productividad y costos
- ¿Cuáles son los desafíos comunes en la implementación del TPM y cómo puedo superarlos con éxito en mi empresa?
- Preguntas frecuentes (FAQ)
¿Qué es el Mantenimiento Productivo Total (TPM) y por qué es importante para mi empresa?
El Mantenimiento Productivo Total (TPM) es una metodología de gestión que tiene como objetivo principal maximizar la eficiencia y confiabilidad de los equipos de producción, al tiempo que se reducen los costos asociados al mantenimiento y las paradas no planificadas. Es una filosofía que busca involucrar a todo el personal de la empresa en el proceso de mejora continua y optimización de la producción.
Implementar el TPM en tu empresa puede tener numerosos beneficios para tu proceso de producción. Algunos de ellos incluyen:
- Reducción de tiempos de inactividad: El TPM ayuda a identificar y corregir problemas antes de que causen una falla o interrupción del equipo, lo que reduce los tiempos de inactividad y aumenta la disponibilidad de los equipos de producción.
- Aumento de la productividad: Mediante la implementación de prácticas de mantenimiento preventivo y predictivo, el TPM permite mantener los equipos en condiciones óptimas de funcionamiento, lo que se traduce en mayor productividad y capacidad de producción.
- Reducción de costos: Al evitar paradas no planificadas y minimizar las averías, el TPM contribuye a reducir los costos asociados al mantenimiento correctivo y al reemplazo de equipos.
- Mejora de la calidad: A través del TPM, se llevan a cabo actividades de inspección y control de calidad de forma regular, lo que ayuda a prevenir defectos y mejorar la calidad de los productos.
- Participación del personal: El TPM implica a todos los miembros de la empresa en el proceso de mejora continua, fomentando la participación activa y el trabajo en equipo.
¿Cuáles son los pilares del Mantenimiento Productivo Total?
El Mantenimiento Productivo Total se basa en ocho pilares fundamentales:
- Pilar de mejora autónoma: Consiste en capacitar a los operarios para que puedan realizar pequeñas tareas de mantenimiento preventivo y supervisar el estado de los equipos.
- Pilar de mantenimiento planificado: Comprende la programación y planificación de las actividades de mantenimiento preventivo y predictivo, así como la gestión de repuestos y recursos necesarios.
- Pilar de mantenimiento especializado: Implica contar con personal capacitado y especializado en el mantenimiento de los equipos, que pueda solucionar problemas más complejos cuando sea necesario.
- Pilar de educación y entrenamiento: Se refiere a la formación constante del personal en prácticas de mantenimiento y mejora continua, así como en el manejo de nuevas tecnologías y técnicas.
- Pilar de control inicial: Consiste en realizar una inspección detallada de los equipos y establecer estándares de funcionamiento, así como definir y eliminar las causas raíz de los problemas.
- Pilar de mantenimiento de calidad: Implica establecer estándares de calidad para los procesos de mantenimiento y realizar inspecciones regulares para garantizar su cumplimiento.
- Pilar de seguridad y medio ambiente: Se centra en la implementación de prácticas seguras de trabajo y la reducción del impacto ambiental de los procesos de producción.
Cuáles son los 8 pilares fundamentales del TPM y cómo puedo implementarlos en mis operaciones
El Mantenimiento Productivo Total (TPM, por sus siglas en inglés) se basa en la idea de que el mantenimiento no debe ser solo una función del departamento de mantenimiento, sino una responsabilidad de todos los miembros de la organización. Para implementar con éxito el TPM, es necesario entender y aplicar los 8 pilares fundamentales:
1. Mejora enfocada
La mejora enfocada implica identificar y eliminar las principales causas de pérdida en el proceso de producción. Esto se logra a través del análisis sistemático de los datos y la implementación de acciones correctivas. Algunas herramientas comunes utilizadas en esta etapa incluyen la metodología de los 5 Porqués y el diagrama de Ishikawa.
2. Mantenimiento autónomo
El mantenimiento autónomo implica capacitar a los operadores para que realicen tareas de mantenimiento básico de manera independiente. Esto incluye la limpieza, inspección, lubricación y ajustes menores de los equipos. Al empoderar a los operadores para que sean responsables de su propio equipo, se pueden identificar y corregir problemas de manera más rápida, reduciendo así las paradas no planificadas.
Algunos aspectos clave del mantenimiento autónomo incluyen la definición de estándares de limpieza y mantenimiento, el seguimiento y la mejora continua de los mismos, y la realización de actividades de capacitación y concienciación.
3. Mejora de equipos
La mejora de equipos implica trabajar en el diseño y la instalación de equipos más eficientes y confiables. Esto se logra a través de la implementación de técnicas como el Análisis de Modo y Efecto de Falla (AMFE) y el Mantenimiento Centrado en Confiabilidad (RCM). El objetivo es minimizar las averías y optimizar el rendimiento y la vida útil de los equipos.
Además, es importante realizar un seguimiento continuo del desempeño de los equipos y realizar mejoras periódicas según sea necesario.
4. Capacitación en habilidades
La capacitación en habilidades tiene como objetivo asegurar que todos los miembros del equipo tengan las habilidades necesarias para realizar sus tareas de manera efectiva. Esto incluye tanto habilidades técnicas relacionadas con el mantenimiento y la operación de los equipos, como habilidades de gestión y liderazgo.
Es importante establecer un programa de capacitación integral que abarque tanto la formación inicial como la formación continua para garantizar que los empleados estén actualizados en las mejores prácticas y las últimas tecnologías.
5. Planificación y programación
La planificación y programación eficaz es fundamental para evitar paradas no planificadas y maximizar la utilización de los recursos. Esto implica desarrollar cronogramas detallados de mantenimiento preventivo, coordinar actividades de mantenimiento con la producción y gestionar de manera proactiva las piezas de repuesto y los insumos necesarios.
También es importante tener procesos claros y definidos para la gestión de emergencias y averías, para poder responder de manera rápida y eficiente ante cualquier inconveniente.
6. Gestión temprana del equipo
La gestión temprana del equipo se refiere a la participación de los equipos de producción en el diseño y desarrollo de nuevos equipos o procesos. Al involucrar a los operadores desde las etapas iniciales, se pueden identificar y corregir posibles problemas antes de la implementación, lo que permite ahorrar tiempo y recursos en el futuro.
Además, esta metodología fomenta la cooperación entre los departamentos de producción y mantenimiento, mejorando así la comunicación y el trabajo en equipo.
7. Compras basadas en TPM
Las compras basadas en TPM implican seleccionar y comprar equipos y materiales que sean confiables, duraderos y fáciles de mantener. Esto implica evaluar la calidad y confiabilidad de los proveedores, así como considerar criterios de mantenibilidad y facilidad de uso al tomar decisiones de compra.
También es importante establecer relaciones sólidas con los proveedores y fomentar una colaboración continua para garantizar un suministro confiable y costos competitivos.
8. Seguridad y medio ambiente
El último pilar del TPM se centra en garantizar un entorno seguro y saludable para los empleados y minimizar el impacto ambiental de las operaciones. Esto implica establecer políticas y prácticas de seguridad robustas, capacitar a los empleados en temas de seguridad y concientización ambiental, y establecer objetivos y programas de mejora que promuevan la sustentabilidad.
Al enfocarse en estos 8 pilares fundamentales y trabajar de manera sistemática para mejorar cada uno de ellos, las organizaciones pueden implementar el TPM de manera efectiva y lograr una producción más eficiente, un mejor rendimiento y una reducción en los costos operativos.
Cómo identificar y eliminar las principales fuentes de pérdida de eficiencia en mi proceso de producción
1. Identificar las fuentes de pérdida
El primer paso para eliminar las fuentes de pérdida de eficiencia en tu proceso de producción es identificar qué aspectos están causando mayores problemas.
Puedes realizar un análisis exhaustivo de tus operaciones y utilizar herramientas como el diagrama de Pareto para determinar qué factores son los más relevantes. Algunas fuentes comunes de pérdida de eficiencia incluyen:
- Fallos en maquinaria: Esto puede incluir averías, mal funcionamiento o falta de mantenimiento adecuado.
- Tiempos de inactividad no planificados: Son aquellos periodos en los que la producción se detiene debido a problemas imprevistos.
- Retrasos en el suministro de materias primas: La falta de materiales necesarios para la producción puede retrasar todo el proceso.
- Defectos en productos: Si hay una alta tasa de productos defectuosos, esto puede afectar negativamente la eficiencia general.
- Tiempos de configuración prolongados: Si cambias de un producto a otro con frecuencia, los tiempos de ajuste prolongados pueden ser una fuente importante de pérdida de tiempo.
Es importante realizar una evaluación completa de tu proceso de producción y analizar cada una de estas áreas para determinar cuál es la fuente principal de pérdida de eficiencia.
2. Establecer métricas de rendimiento
Una vez que hayas identificado las fuentes de pérdida, es fundamental establecer métricas de rendimiento claras y medibles para evaluar su impacto.
Estas métricas pueden incluir cosas como el tiempo medio entre fallos (MTBF), el tiempo medio de reparación (MTTR), la tasa de productos defectuosos o cualquier otro indicador relevante para tu proceso de producción.
Al establecer estas métricas, podrás medir el progreso a medida que implementes cambios y mejoras en tu proceso. También te ayudarán a identificar áreas específicas que requieren una atención más inmediata.
3. Analizar y eliminar las fuentes de pérdida
Una vez que hayas identificado las fuentes de pérdida y establecido tus métricas de rendimiento, podrás comenzar a analizar cada una de ellas y tomar acciones para eliminarlas.
Para abordar los fallos en maquinaria, por ejemplo, podrías implementar un programa de mantenimiento preventivo regular y establecer protocolos para la correcta operación y limpieza de las máquinas. Si los retrasos en el suministro de materias primas son un problema, podrías considerar trabajar más estrechamente con tus proveedores para mejorar la eficiencia logística.
Es importante que estas acciones sean específicas y medibles, y que continúes evaluando su impacto utilizando tus métricas de rendimiento. De esta manera, podrás hacer ajustes según sea necesario y asegurarte de que estás progresando hacia la eliminación total de las fuentes de pérdida de eficiencia.
4. Implementar un sistema de mantenimiento productivo total (TPM)
El mantenimiento productivo total, o TPM, es una filosofía que se centra en la implicación de todos los miembros de la organización en el mantenimiento y mejora continua de los equipos y procesos de producción.
Para implementar TPM, debes establecer una cultura de cuidado y responsabilidad compartida en toda la empresa. Esto implica capacitar a los operarios para realizar tareas de mantenimiento básicas, fomentar la comunicación entre los diferentes departamentos y promover la colaboración para identificar y solucionar problemas.
Además, TPM también se basa en la idea de minimizar las pérdidas mediante el establecimiento de planes de mantenimiento preventivo, la mejora de los tiempos de configuración y la creación de equipos multifuncionales encargados de resolver problemas específicos.
Implementar un sistema de TPM requiere tiempo y dedicación, pero puede tener un impacto significativo en la eficiencia de tu proceso de producción.
Cuál es el papel de la gestión del mantenimiento en el TPM y cómo puedo mejorarla en mi empresa
La gestión del mantenimiento juega un papel crucial en la implementación exitosa del Mantenimiento Productivo Total (TPM) en una empresa. El TPM es un enfoque holístico para mejorar la eficiencia y la confiabilidad de los equipos y procesos de producción, y la gestión del mantenimiento desempeña un papel clave en este proceso.
La gestión del mantenimiento se centra en la implementación de estrategias y prácticas efectivas para mantener y mejorar los activos físicos de una empresa. Esto incluye la planificación y programación de actividades de mantenimiento, la gestión de los recursos necesarios, la supervisión y control de las operaciones de mantenimiento, y la implementación de estrategias de mejora continua.
Para mejorar la gestión del mantenimiento en el contexto del TPM, es importante tener en cuenta varios aspectos clave. En primer lugar, es fundamental establecer un plan de mantenimiento preventivo adecuado. Esto implica identificar los equipos críticos en términos de su impacto en la productividad y confiabilidad de la planta, y desarrollar programas de mantenimiento preventivo específicos para estos equipos.
Además, es crucial implementar un sistema de registro y seguimiento de las actividades de mantenimiento. Esto permite rastrear y analizar los datos relacionados con el rendimiento de los equipos, los tiempos de inactividad y las razones de las fallas, lo que a su vez ayuda a identificar y corregir los problemas recurrentes.
Otro aspecto importante es capacitar al personal de mantenimiento de manera adecuada. Es esencial que los miembros del equipo de mantenimiento estén debidamente capacitados y tengan el conocimiento y las habilidades necesarias para llevar a cabo las actividades de mantenimiento de manera efectiva. Esto incluye conocer los procedimientos de mantenimiento adecuados, saber utilizar las herramientas y equipos correctamente y comprender los conceptos básicos del TPM y su aplicación práctica.
Además, es recomendable fomentar una cultura de mejora continua dentro del departamento de mantenimiento. Esto implica animar al personal a buscar constantemente formas de mejorar los procesos y prácticas de mantenimiento, y proporcionarles las herramientas y recursos necesarios para hacerlo. Establecer equipos de mejora y promover la participación activa de todos los miembros del equipo en la identificación y resolución de problemas también puede ser beneficioso en este sentido.
Mejorar la gestión del mantenimiento en el contexto del TPM implica establecer un plan de mantenimiento preventivo eficaz, implementar un sistema de registro y seguimiento de las actividades de mantenimiento, capacitar al personal de manera adecuada y fomentar una cultura de mejora continua. Al hacerlo, las empresas pueden maximizar la eficiencia y confiabilidad de sus equipos y procesos de producción, lo que a su vez les permitirá reducir costos y aumentar su rentabilidad.
Qué herramientas y técnicas puedo utilizar para optimizar el tiempo de actividad de mis activos y reducir los tiempos de paro no planificados
El Mantenimiento Productivo Total (TPM) es una metodología que se basa en utilizar herramientas y técnicas específicas para optimizar el tiempo de actividad de los activos y reducir los tiempos de paro no planificados.
Análisis de Modo y Efecto de Fallas (FMEA)
El análisis FMEA es una herramienta utilizada para identificar y priorizar las fallas en los equipos o procesos, y determinar su potencial impacto en la producción. Consiste en analizar los modos de fallo posibles, sus efectos y la frecuencia con la que ocurren. Con esta información, se pueden tomar acciones preventivas antes de que ocurran las fallas.
Mantenimiento Preventivo
El mantenimiento preventivo implica realizar inspecciones periódicas, limpieza, lubricación y reemplazo de componentes de los equipos antes de que se produzcan fallas. Esto ayuda a mantener los equipos en óptimas condiciones de funcionamiento y evita tiempos de paro no planificados.
Mantenimiento Predictivo
El mantenimiento predictivo utiliza tecnologías avanzadas como la monitorización de vibraciones, termografía, análisis de aceite, entre otras, para predecir fallas en los equipos antes de que ocurran. Estas técnicas permiten detectar señales tempranas de problemas y así poder tomar acciones preventivas en el momento adecuado.
Mantenimiento Autónomo
El mantenimiento autónomo involucra a los operadores en la tarea de mantenimiento básico de los equipos. Esto incluye limpieza, lubricación, inspección visual y detección temprana de problemas. Al empoderar a los operadores para que sean responsables del mantenimiento de sus propios equipos, se promueve la sensibilización y el cuidado de los activos.
Cambio Rápido de Herramientas (SMED)
El SMED es una técnica utilizada para reducir el tiempo necesario para realizar cambios entre diferentes productos o tareas en una línea de producción. Esto se logra mediante la identificación y eliminación de pasos innecesarios, reducción del tiempo de ajuste y mejora de los procesos de preparación. Un cambio rápido de herramientas permite reducir los tiempos de paro y aumentar la eficiencia de la producción.
Gestión del Mantenimiento
Una buena gestión del mantenimiento es fundamental para optimizar el tiempo de actividad de los activos. Esto implica llevar registros precisos de las actividades de mantenimiento, programar actividades de forma eficiente, gestionar el inventario de repuestos y garantizar la capacitación adecuada del personal de mantenimiento.
Formación y Capacitación
La formación y capacitación son esenciales para implementar el TPM de manera efectiva. Los equipos de trabajo deben estar familiarizados con las técnicas y herramientas del TPM, así como con los objetivos y beneficios que se pueden obtener. La capacitación constante ayuda a mantener al personal actualizado y comprometido con el proceso de mejora continua.
Gestión del Cambio
Implementar el TPM requiere un cambio en la cultura organizacional y en las prácticas de trabajo. Es importante contar con un enfoque sistemático para gestionar el cambio, que incluya la comunicación efectiva, la participación activa de los empleados y la superación de posibles resistencias. La gestión del cambio permite asegurar una transición exitosa hacia una cultura de TPM.
Al utilizar estas herramientas y técnicas del TPM, podrás optimizar el tiempo de actividad de tus activos y reducir los tiempos de paro no planificados. El resultado será una mejora en la eficiencia de la producción, mayor confiabilidad de los equipos y reducción de costos operativos.
Cómo realizar un análisis de la eficacia global del equipo (OEE) y utilizarlo como indicador clave de rendimiento en el TPM
El análisis de la eficacia global del equipo (OEE) es una métrica clave en el TPM, ya que proporciona información sobre cómo se está utilizando el equipo y qué tan eficientemente se está produciendo. El OEE se calcula mediante la multiplicación de tres factores principales: disponibilidad, rendimiento y calidad.
Para comenzar a realizar un análisis de OEE, primero debes identificar cuánto tiempo está disponible el equipo para producir. Esto se conoce como tiempo disponible o tiempo base. Es importante tener en cuenta que este tiempo no incluye las paradas planificadas, como el tiempo destinado a mantenimiento preventivo.
A continuación, debes identificar cuánto tiempo se utiliza realmente para producir, lo cual se conoce como tiempo neto. Esto incluye el tiempo en el que el equipo está funcionando efectivamente y produciendo productos de calidad. El tiempo neto debe excluir todas las paradas no planificadas, como paros por averías o cambios de producto.
Una vez que tengas estos dos tiempos, puedes calcular la disponibilidad mediante la fórmula:
Disponibilidad = Tiempo neto / Tiempo base
La disponibilidad te ayuda a identificar qué tan bien se está utilizando el equipo. Puedes ajustar este cálculo tomando en cuenta las paradas planificadas si así lo deseas.
El siguiente factor para calcular el OEE es el rendimiento, que se refiere a qué tan eficientemente se está produciendo durante el tiempo neto. Para calcular el rendimiento, necesitas conocer la capacidad nominal del equipo durante el tiempo neto, es decir, cuánto podría producirse si el equipo estuviera funcionando al 100% sin detenerse.
Cuáles son las mejores prácticas para establecer rutinas de mantenimiento preventivo y predictivo en el marco del TPM
Establecer rutinas de mantenimiento preventivo y predictivo es una parte fundamental del Mantenimiento Productivo Total (TPM). Estas prácticas permiten mantener los equipos en óptimas condiciones, prevenir fallas y reducir los tiempos de inactividad no planificados. A continuación, te compartimos las mejores prácticas para establecer rutinas efectivas de mantenimiento en el marco del TPM:
1. Evaluación inicial
Antes de implementar rutinas de mantenimiento preventivo y predictivo, es importante realizar una evaluación inicial de los equipos y las instalaciones. Esto incluye identificar los activos críticos, analizar su estado actual, identificar los puntos débiles y determinar las estrategias adecuadas de mantenimiento. La evaluación inicial proporcionará una base sólida para establecer rutinas efectivas.
2. Planificación de las rutinas
Una vez realizada la evaluación inicial, es necesario desarrollar un plan detallado de las rutinas de mantenimiento. Esto implica definir los intervalos de frecuencia, las tareas específicas a realizar, los recursos necesarios y los responsables de llevar a cabo cada actividad. La planificación debe ser precisa y considerar tanto el tiempo disponible como las restricciones operativas.
3. Gestión de los activos
Un componente clave del mantenimiento preventivo y predictivo es la gestión de los activos. Esto implica llevar un registro detallado de todos los equipos, incluyendo su ubicación, características técnicas, historial de mantenimiento y vida útil estimada. También es importante implementar un sistema de monitoreo continuo para detectar posibles problemas de manera temprana y tomar acciones correctivas.
4. Capacitación del personal
Es fundamental capacitar al personal encargado de llevar a cabo las rutinas de mantenimiento preventivo y predictivo. Esto incluye proporcionarles la formación necesaria sobre los equipos, las técnicas de mantenimiento y las herramientas utilizadas. Además, se debe fomentar la participación activa del personal en la identificación de mejoras y en la resolución de problemas relacionados con el mantenimiento.
5. Seguimiento y mejora continua
Una vez establecidas las rutinas de mantenimiento, es importante realizar un seguimiento constante de su efectividad. Esto implica recolectar y analizar datos relacionados con la frecuencia de fallos, los indicadores de desempeño y los costos asociados al mantenimiento. Con base en estos análisis, se pueden implementar mejoras continuas para optimizar las rutinas y maximizar la eficiencia y confiabilidad de los equipos.
Establecer rutinas de mantenimiento preventivo y predictivo en el marco del TPM requiere de una evaluación inicial exhaustiva, una planificación detallada, una gestión efectiva de los activos y una capacitación adecuada del personal. Además, es necesario realizar un seguimiento constante y buscar oportunidades de mejora continua. Siguiendo estas mejores prácticas, podrás mejorar tu producción, reducir los costos y aumentar la confiabilidad de tus equipos.
Cómo formar y capacitar a mi equipo de trabajo para que esté alineado con los principios y objetivos del TPM
Formar y capacitar a tu equipo de trabajo es fundamental para asegurar que estén alineados con los principios y objetivos del TPM. Aquí te brindaremos algunas recomendaciones sobre cómo hacerlo de manera efectiva.
1. Comunicación clara de los objetivos
Es importante que tus empleados comprendan claramente cuáles son los objetivos del TPM y cómo su trabajo contribuye a alcanzarlos. Realiza reuniones y sesiones de capacitación en las que puedas explicarles de manera clara y concisa cuál es el propósito del mantenimiento productivo total y qué se espera de cada uno de ellos.
2. Capacitación técnica
El TPM requiere de habilidades técnicas específicas, por lo tanto, debes asegurarte de que tu equipo de trabajo reciba la capacitación necesaria. Puedes organizar cursos, talleres o conferencias impartidas por expertos en TPM para brindarles los conocimientos y herramientas necesarios para implementarlo de manera efectiva.
3. Fomento de la participación activa
Involucrar a tu equipo de trabajo en la toma de decisiones y en la identificación de problemas es fundamental para lograr una implementación exitosa del TPM. Anima a tus empleados a expresar sus ideas y opiniones, y establece un ambiente en el que se sientan seguros de hacerlo.
4. Establecimiento de metas y seguimiento
Define metas claras y alcanzables relacionadas con el TPM y asegúrate de que tengas un sistema de seguimiento para evaluar su progreso. Mantén un registro de los logros y reconoce el esfuerzo de tu equipo cuando alcancen sus objetivos.
5. Retroalimentación constante
Proporcionar retroalimentación regular a tu equipo de trabajo es esencial para su desarrollo y mejora continua. Haz seguimiento periódico de su desempeño, ofrece comentarios constructivos y reconoce sus logros. Esto ayudará a mantener su motivación y compromiso con el TPM.
Formar y capacitar a tu equipo de trabajo en los principios y objetivos del TPM es una inversión clave para el éxito de su implementación. Asegúrate de comunicar claramente los objetivos, brindar la capacitación técnica necesaria, fomentar la participación activa, establecer metas claras y proporcionar retroalimentación constante. Con un equipo alineado y bien preparado, podrás mejorar la producción y reducir costos de manera significativa.
Qué beneficios puedo obtener al implementar el TPM en mi empresa y cómo puedo medir su impacto en la productividad y costos
Implementar el Mantenimiento Productivo Total (TPM) en tu empresa puede generar una serie de beneficios significativos tanto en términos de productividad como de reducción de costos. A continuación, se presentan algunos de los beneficios clave que puedes obtener al implementar el TPM:
1. Mejora de la eficiencia y disponibilidad de los equipos
El TPM se centra en mantener los equipos en óptimas condiciones a través de acciones preventivas y rutinas de mantenimiento planificadas. Esto permite minimizar las fallas repentinas y prolongar la vida útil de los equipos, lo que aumenta su disponibilidad y reduce los tiempos de inactividad.
2. Aumento de la productividad y reducción de los tiempos de paro
Al mejorar la eficiencia y disponibilidad de los equipos, el TPM permite reducir los tiempos de paro no planificados, lo que a su vez aumenta la producción y la eficiencia general de las operaciones. Además, el TPM también fomenta la participación activa de los empleados en la detección y resolución de problemas, lo que ayuda a agilizar los procesos y optimizar la utilización de los recursos disponibles.
3. Reducción de los costos de mantenimiento y reparación
El TPM busca prevenir las fallas y realizar mantenimientos correctivos antes de que se vuelvan críticos. Esto reduce la necesidad de reparaciones costosas y minimiza los gastos asociados al mantenimiento, como la compra de piezas de repuesto de emergencia y la contratación de servicios externos. Asimismo, al prolongar la vida útil de los equipos, se reduce la necesidad de invertir en nuevas adquisiciones a corto plazo.
4. Mejora de la calidad del producto
El TPM también tiene un impacto positivo en la calidad del producto final. Al mantener los equipos en buenas condiciones, se reducen los defectos y errores de producción, lo que se traduce en productos de mayor calidad y menores costos de reproceso o retrabajo.
Medición del impacto del TPM en la productividad y costos
Para medir el impacto del TPM en la productividad y los costos, es importante establecer indicadores clave de rendimiento (KPIs) que reflejen los beneficios esperados. Algunos KPIs comunes utilizados para evaluar el éxito del TPM incluyen:
- Tiempo de disponibilidad de los equipos
- Tiempo medio entre las fallas
- Tiempo medio para reparar las fallas
- Tiempo de inactividad no planificado
- Tasa de defectos en la producción
- Tiempo de preparación de las máquinas o cambio de productos
Estos indicadores pueden ser monitoreados regularmente y comparados con los valores previos a la implementación del TPM para evaluar el progreso y determinar el impacto real en la productividad y los costos. Además, es importante involucrar a los empleados y solicitar su retroalimentación para obtener una visión más completa de los resultados.
¿Cuáles son los desafíos comunes en la implementación del TPM y cómo puedo superarlos con éxito en mi empresa?
Implementar el Mantenimiento Productivo Total (TPM) en una empresa puede resultar todo un desafío. Aunque los beneficios de hacerlo pueden ser enormes, como mejorar la producción y reducir costos, es importante entender los obstáculos comunes que se pueden encontrar en el camino y cómo superarlos con éxito.
Falta de compromiso de la alta dirección
Uno de los mayores obstáculos en la implementación del TPM es la falta de compromiso por parte de la alta dirección. Sin su apoyo y liderazgo, el proceso puede no tener la fuerza necesaria para ser exitoso. Es esencial contar con el respaldo de la dirección y que ellos mismos sean partícipes activos en el cambio.
Falta de recursos y capacitación adecuada
Para implementar correctamente el TPM, es fundamental contar con los recursos necesarios, tanto humanos como tecnológicos. Además, es importante brindar la capacitación adecuada a todos los involucrados en el proceso. Esto asegurará que cada miembro del equipo tenga las habilidades y conocimientos necesarios para llevar a cabo las tareas de mantenimiento de manera efectiva.
Falta de participación e involucramiento de los empleados
La implementación exitosa del TPM requiere la participación y el involucramiento activo de todos los miembros de la organización, desde los operadores hasta los altos directivos. Sin embargo, puede haber resistencia al cambio y falta de colaboración por parte de algunos empleados. Es vital fomentar una cultura de trabajo en equipo y motivar a todos los miembros de la organización a participar en el proceso de implementación.
Falta de seguimiento y evaluación continua
Una vez iniciada la implementación del TPM, es imprescindible llevar a cabo un seguimiento constante y realizar evaluaciones periódicas para medir los resultados obtenidos y corregir cualquier desviación o problema que pueda surgir. La falta de seguimiento y evaluación continua puede llevar al estancamiento del proceso y dejar de aprovechar oportunidades de mejora.
Falta de comunicación efectiva
La comunicación efectiva es clave durante todo el proceso de implementación del TPM. Es necesario compartir información y objetivos claros con todos los involucrados, fomentar la retroalimentación y mantener un canal abierto de comunicación entre los diferentes niveles jerárquicos. La falta de comunicación puede generar confusión, malentendidos y obstaculizar el avance del proyecto.
Superar los desafíos comunes en la implementación del TPM requiere un fuerte compromiso de la dirección, asignación adecuada de recursos, participación activa de los empleados, seguimiento continuo y comunicación efectiva. Al abordar estos obstáculos de manera proactiva, se podrá lograr una implementación exitosa del TPM y disfrutar de los beneficios que esto conlleva para la producción y los costos de la empresa.
Preguntas frecuentes (FAQ)
1. ¿Qué es el Mantenimiento Productivo Total?
El Mantenimiento Productivo Total (TPM) es una metodología de gestión que se enfoca en mejorar la eficiencia y confiabilidad de los equipos y procesos productivos.
2. ¿Cuáles son los beneficios del TPM?
El TPM ayuda a reducir los costos de mantenimiento, aumentar la productividad, mejorar la calidad del producto y optimizar la utilización de recursos.
3. ¿Cómo se implementa el TPM en una empresa?
La implementación del TPM requiere de un compromiso de toda la organización, estableciendo equipos de trabajo dedicados al mantenimiento y promoviendo una cultura de autogestión y mejora continua.
4. ¿Cuál es la diferencia entre el TPM y el mantenimiento preventivo?
A diferencia del mantenimiento preventivo, que se enfoca en realizar acciones de forma planificada para evitar fallas, el TPM busca maximizar la eficiencia y rendimiento de los equipos a través de la participación activa de todos los miembros de la organización.
5. ¿Es el TPM aplicable solo a empresas de manufactura?
No, el TPM se puede aplicar en cualquier tipo de organización, ya sea de manufactura, servicios u otros sectores. El objetivo principal es mejorar la productividad y reducir los costos de mantenimiento en cualquier tipo de proceso.
Deja una respuesta
Entradas relacionadas