Descubre cómo implementar Kaizen y Lean Manufacturing para maximizar la eficiencia de tu empresa
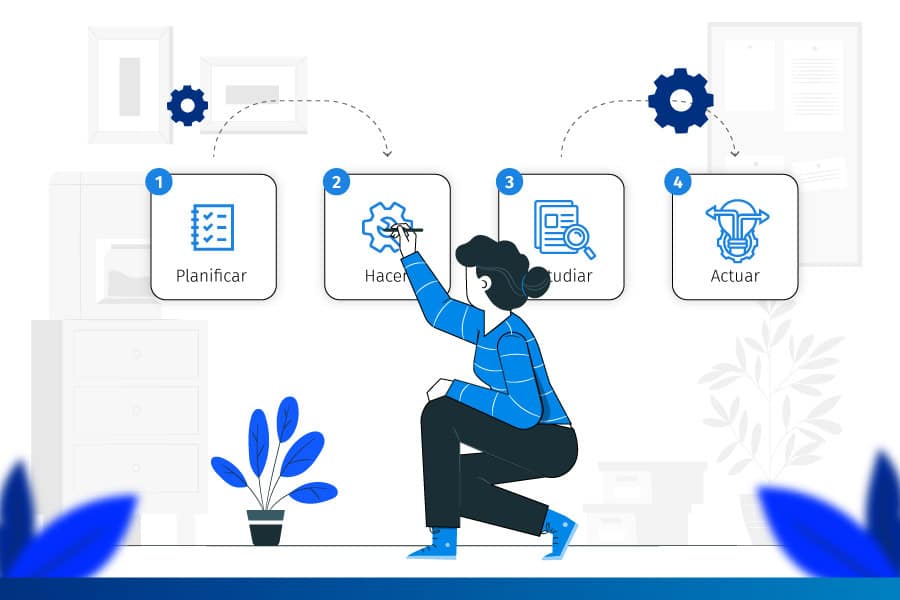
En un mercado global altamente competitivo, las empresas buscan constantemente mejorar su productividad y eficiencia para mantenerse a la vanguardia. Dos metodologías muy populares para lograr esto son el Kaizen y el Lean Manufacturing.
El Kaizen es una filosofía de mejora continua que se enfoca en eliminar el desperdicio y optimizar los procesos. Por otro lado, el Lean Manufacturing es una metodología centrada en la reducción del tiempo y recursos utilizados en la producción. Ambas tienen como objetivo principal maximizar la eficiencia y minimizar los costos en una empresa.
- Qué es Kaizen y cómo puede beneficiar a mi empresa
- Cuáles son los principios básicos del Lean Manufacturing
- Qué pasos debo seguir para implementar Kaizen en mi empresa
- Paso 1: Crear una cultura de mejora continua
- Paso 2: Establecer un equipo de Kaizen
- Paso 3: Realizar un análisis exhaustivo de los procesos
- Paso 4: Definir objetivos y metas claras
- Paso 5: Implementar soluciones y realizar seguimiento
- Paso 6: Capacitar y educar a todos los empleados
- Paso 7: Celebrar los éxitos y reconocer el esfuerzo
- Cómo puedo aplicar los conceptos de Lean Manufacturing en mi cadena de producción
- Cuáles son las herramientas y técnicas más utilizadas en Kaizen y Lean Manufacturing
- Cuál es el impacto de la filosofía Kaizen en la cultura de mi empresa
- Dónde puedo encontrar recursos y formación para implementar Kaizen y Lean Manufacturing
- Cuáles son algunos casos de éxito de empresas que han implementado Kaizen y Lean Manufacturing
- Cómo puedo evaluar y medir los resultados de la implementación de Kaizen y Lean Manufacturing en mi empresa
- Cuáles son los desafíos comunes al implementar Kaizen y Lean Manufacturing y cómo superarlos
Qué es Kaizen y cómo puede beneficiar a mi empresa
El Kaizen es una metodología japonesa que se enfoca en la mejora continua de los procesos y actividades dentro de una empresa. Su objetivo principal es eliminar los desperdicios y maximizar la eficiencia, logrando así una mayor productividad y calidad en los productos o servicios que ofrece la organización.
La filosofía del Kaizen se basa en la participación activa de todos los miembros de la empresa, desde los trabajadores de línea hasta la alta dirección. Todos son responsables de identificar oportunidades de mejora y proponer soluciones para optimizar los procesos.
Para implementar el Kaizen en una organización, es necesario seguir una serie de pasos. En primer lugar, es fundamental establecer un ambiente propicio para el cambio, en donde todos los empleados se sientan comprometidos y motivados a mejorar. También es necesario capacitar al personal en las herramientas y técnicas del Kaizen, como el uso de los 5S, el análisis de flujo de valor y las reuniones de mejora.
Otra clave para implementar el Kaizen de manera efectiva es establecer indicadores de desempeño para medir los avances y verificar si se están logrando los objetivos planteados. Estos indicadores pueden ser el tiempo de ejecución de un proceso, el número de productos defectuosos o la satisfacción del cliente, entre otros.
Es importante destacar que el Kaizen no busca realizar cambios drásticos y a gran escala, sino más bien pequeñas mejoras incrementales y constantes. De esta forma, se evitan los riesgos y resistencias asociadas a los cambios radicales, y se asegura un proceso de mejora continua sostenible en el tiempo.
Cuáles son los principios básicos del Lean Manufacturing
El Lean Manufacturing se basa en una serie de principios clave que buscan eliminar el desperdicio, maximizar la eficiencia y optimizar los procesos en una empresa. Estos principios son fundamentales para implementar con éxito esta metodología y obtener resultados significativos.
1. Identificación del valor
El primer paso en Lean Manufacturing es identificar qué es lo que agrega valor para el cliente. Esto implica comprender las necesidades y expectativas del cliente y evaluar cómo se pueden satisfacer de manera efectiva. Al identificar el valor, se pueden eliminar actividades que no agregan valor y enfocarse en aquellas que sí lo hacen.
2. Mapeo de flujo de valor
Una vez que se ha identificado el valor, se debe realizar un mapeo exhaustivo del flujo de valor, es decir, analizar todas las actividades y procesos para producir y entregar ese valor al cliente. El objetivo es eliminar cualquier tipo de desperdicio o actividad innecesaria que pueda estar retrasando o afectando la eficiencia del proceso.
3. Creación del flujo continuo
Una vez que se ha mapeado el flujo de valor, el siguiente paso es crear un flujo continuo, es decir, establecer un sistema en el que los productos o servicios fluyan de manera constante y sin interrupciones a través de cada etapa del proceso. Esto implica eliminar cualquier tipo de cuellos de botella o retrasos que puedan estar limitando la eficiencia y la capacidad de respuesta.
4. Establecimiento del tirón (pull)
El principio del tirón implica que solo se debe producir aquello que se demande, en lugar de producir en exceso y acumular inventario. Esto ayuda a minimizar el desperdicio y garantizar que se produzca lo justo y necesario para satisfacer las necesidades reales del cliente.
5. Perfección continua
El Lean Manufacturing se basa en la idea de la mejora continua y la búsqueda constante de la perfección. Esto implica establecer sistemas de retroalimentación y aprendizaje, realizar análisis y evaluaciones periódicas, así como implementar medidas correctivas para eliminar cualquier tipo de problema o desperdicio identificado.
Al seguir estos principios básicos del Lean Manufacturing, las empresas pueden lograr una mayor eficiencia en sus procesos, reducir costos, mejorar la calidad y entregar productos o servicios de valor agregado a sus clientes.
Qué pasos debo seguir para implementar Kaizen en mi empresa
Implementar Kaizen en tu empresa puede ser un proceso que requiere tiempo y dedicación, pero los beneficios a largo plazo hacen que valga la pena. Aquí te presentamos algunos pasos clave que debes seguir para implementar con éxito Kaizen en tu empresa:
Paso 1: Crear una cultura de mejora continua
El primer paso para implementar Kaizen es crear una cultura de mejora continua en toda la organización. Esto implica fomentar la participación y el compromiso de todos los empleados en la búsqueda constante de mejoras en los procesos, productos y servicios.
Paso 2: Establecer un equipo de Kaizen
Es fundamental contar con un equipo dedicado exclusivamente a la implementación de Kaizen en la empresa. Este equipo será responsable de liderar el cambio, identificar oportunidades de mejora, llevar a cabo análisis de los procesos existentes y proponer soluciones eficientes.
Paso 3: Realizar un análisis exhaustivo de los procesos
Antes de comenzar cualquier proyecto de mejora, es importante realizar un análisis exhaustivo de los procesos existentes. Esto implica identificar las áreas de mayor desperdicio, ineficiencia o problemas recurrentes que necesitan mejoras. El equipo de Kaizen se encargará de recopilar y analizar los datos relevantes.
Paso 4: Definir objetivos y metas claras
Una vez identificadas las áreas de mejora, es necesario establecer objetivos y metas claras para cada proyecto Kaizen. Estos objetivos deben ser medibles, alcanzables y alineados con los objetivos estratégicos de la empresa.
Paso 5: Implementar soluciones y realizar seguimiento
Una vez que se hayan definido los proyectos de mejora, es hora de implementar las soluciones propuestas. Esto implica realizar cambios tanto en los procesos como en la cultura organizacional. Es importante establecer indicadores clave de desempeño para medir el impacto de las mejoras y realizar un seguimiento regular para asegurarse de que los resultados esperados se estén logrando.
Paso 6: Capacitar y educar a todos los empleados
La implementación de Kaizen requiere una mentalidad de aprendizaje constante y una participación activa de todos los empleados. Es importante capacitar y educar a todos los miembros de la organización sobre los principios y herramientas de Kaizen para que puedan contribuir de manera efectiva a la mejora continua.
Paso 7: Celebrar los éxitos y reconocer el esfuerzo
Es fundamental celebrar los éxitos y reconocer el esfuerzo de los empleados involucrados en los proyectos Kaizen. Esto ayuda a mantener la motivación y el compromiso de todos los miembros de la organización, y refuerza la cultura de mejora continua.
Seguir estos pasos te ayudará a implementar con éxito Kaizen en tu empresa y maximizar su eficiencia a largo plazo. Recuerda que la implementación de Kaizen es un proceso continuo y nunca terminado, por lo que es importante mantener el enfoque en la mejora continua y adaptarse a los cambios constantes del entorno empresarial.
Cómo puedo aplicar los conceptos de Lean Manufacturing en mi cadena de producción
Para implementar los conceptos de Lean Manufacturing en tu cadena de producción, es importante seguir una serie de pasos y adoptar ciertas prácticas que te ayudarán a maximizar la eficiencia de tu empresa. A continuación, te presento algunas recomendaciones clave:
1. Identificar el valor para el cliente
El primer paso en la implementación de Lean Manufacturing es identificar qué actividades y procesos son realmente valiosos para el cliente. Esto implica comprender las necesidades y expectativas del cliente, para así poder enfocar los esfuerzos en aquellas áreas que generen un mayor impacto.
2. Mapear el flujo de valor
Una vez identificado el valor para el cliente, es necesario realizar un mapeo del flujo de valor actual de la cadena de producción. Esto implica analizar en detalle todos los pasos y procesos involucrados desde que se recibe la materia prima hasta que se entrega el producto final al cliente. Esta etapa permitirá identificar posibles desperdicios y oportunidades de mejora.
3. Eliminar los desperdicios
Una de las principales premisas del Lean Manufacturing es eliminar todo lo que no agrega valor al producto o servicio. Para lograr esto, es necesario identificar los diferentes tipos de desperdicios (como el exceso de inventario, tiempos de espera, procesos innecesarios, etc.) y trabajar en su reducción o eliminación. Esto ayudará a mejorar la eficiencia y reducir costos.
4. Establecer sistemas de mejora continua
El Kaizen, que significa "mejora continua" en japonés, es una parte fundamental del Lean Manufacturing. Se trata de establecer procesos y sistemas que fomenten la mejora constante en todos los niveles de la organización. Esto implica involucrar a todos los empleados, alentar la generación de ideas y soluciones, y llevar a cabo evaluaciones periódicas para medir el progreso.
5. Implementar herramientas Lean
Existen diversas herramientas y técnicas que pueden ser utilizadas para implementar Lean Manufacturing, como el Just in Time (JIT), el Kanban, el Single-Minute Exchange of Die (SMED), entre otras. Estas herramientas ayudan a optimizar la planificación, reducir el tiempo de ciclo, mejorar la calidad y aumentar la flexibilidad.
6. Capacitar al personal
Es fundamental capacitar a todo el personal involucrado en la cadena de producción para que comprendan los principios y metodologías del Lean Manufacturing. Esto les permitirá identificar oportunidades de mejora, trabajar de manera colaborativa y mantener un enfoque constante en la eficiencia.
Implementar los conceptos de Lean Manufacturing puede llevar tiempo y requerir cambios significativos en la forma en que se realizan las tareas diarias. Sin embargo, los beneficios obtenidos, como la reducción de costos, la mejora de la calidad y la satisfacción del cliente, hacen que valga la pena el esfuerzo.
Cuáles son las herramientas y técnicas más utilizadas en Kaizen y Lean Manufacturing
En el mundo del Kaizen y Lean Manufacturing, existen diversas herramientas y técnicas que se utilizan para maximizar la eficiencia de las empresas. A continuación, te presentamos algunas de las más utilizadas:
1. Valor agregado
El enfoque principal del Kaizen y Lean Manufacturing es eliminar todos los procesos que no agregan valor al producto o servicio final. La técnica de valor agregado ayuda a identificar cuáles son esos procesos y trabajar en su eliminación o mejora.
2. Mapeo de flujo de valor (VSM)
El mapeo de flujo de valor (VSM) es una herramienta visual que permite identificar todas las actividades, desde el pedido del cliente hasta la entrega del producto. Permite detectar los desperdicios y tiempos muertos en el proceso y buscar formas de eliminarlos o minimizarlos.
3. 5S
Las 5S son una metodología japonesa que busca mantener el área de trabajo limpia, ordenada y organizada. Las cinco etapas de las 5S son: clasificar, organizar, limpiar, estandarizar y disciplina. Esta técnica ayuda a eliminar la pérdida de tiempo buscando herramientas o materiales y mejorar la seguridad en el lugar de trabajo.
4. Just in Time (JIT)
La técnica Just in Time (JIT) busca reducir los inventarios al mínimo necesario y entregar los productos justo en el momento en que se necesitan. Esto evita la acumulación de inventarios obsoletos y reduce los costos asociados.
5. Poka Yoke
Poka Yoke se refiere a los mecanismos que se utilizan para prevenir errores o defectos durante el proceso de producción. Estos mecanismos pueden ser físicos (como sensores o alarmas) o visuales (como instrucciones claras y fáciles de seguir).
6. Kanban
Kanban es un sistema visual utilizado para gestionar el flujo de trabajo y la producción. Utiliza tarjetas o etiquetas que representan las tareas a realizar y permite controlar el progreso de cada tarea y evitar la sobrecarga de trabajo.
7. Mejora continua
La mejora continua es el alma del Kaizen y Lean Manufacturing. Consiste en buscar constantemente formas de optimizar los procesos y reducir los desperdicios. Para ello, se utilizan técnicas como las lluvias de ideas, análisis de causa raíz y la implementación de cambios pequeños pero constantes.
8. Six Sigma
Six Sigma es una metodología que busca mejorar la calidad al reducir la variabilidad en los procesos. Se basa en el análisis estadístico de datos y utiliza herramientas como el DMAIC (Definir, Medir, Analizar, Mejorar y Controlar) para alcanzar resultados de alta calidad.
9. Jidoka
Jidoka es una técnica que busca automatizar la detección de problemas y errores en la línea de producción. Esta técnica permite la intervención humana inmediata cuando se detecta un problema, evitando así la producción de productos defectuosos.
10. Participación y empoderamiento de los empleados
En el Kaizen y Lean Manufacturing, se valora la participación activa de todos los empleados en la mejora continua de la empresa. Se fomenta el empoderamiento de los empleados para que puedan identificar problemas y proponer soluciones.
Estas son solo algunas de las herramientas y técnicas más utilizadas en Kaizen y Lean Manufacturing. La elección de las herramientas a utilizar dependerá de las necesidades y objetivos específicos de cada empresa.
Cuál es el impacto de la filosofía Kaizen en la cultura de mi empresa
La filosofía Kaizen se basa en la idea de la mejora continua, donde los empleados y la empresa trabajan juntos para identificar y eliminar desperdicios, optimizar procesos y buscar constantemente formas de mejorar el rendimiento y la eficiencia. Cuando se implementa correctamente, Kaizen puede tener un impacto significativo en la cultura de una empresa.
Una de las principales formas en que Kaizen afecta a la cultura de la empresa es fomentando un ambiente de trabajo en equipo y colaboración. Bajo la filosofía de Kaizen, todos los miembros de la organización, desde el nivel más alto de la dirección hasta los trabajadores de producción, están involucrados en la identificación y resolución de problemas. Esto implica que todos deben trabajar juntos y compartir ideas y soluciones para lograr mejoras continuas.
Además, Kaizen promueve el empoderamiento de los empleados al darles la autoridad y la responsabilidad de tomar decisiones y hacer cambios en sus propias áreas de trabajo. Esto estimula la creatividad y la innovación, ya que los empleados son alentados a proponer nuevas ideas y soluciones para mejorar los procesos y reducir los desperdicios.
Otro elemento importante de la cultura Kaizen es la búsqueda constante de la excelencia y la mejora. Los empleados deben estar dispuestos a cuestionar el status quo y a desafiar las prácticas existentes para encontrar formas más eficientes de hacer las cosas. Esta actitud de siempre encontrar formas mejores y más eficientes de funcionar se convierte en parte de la forma en que la empresa opera, impulsando no solo la mejora de los procesos sino también la innovación y el crecimiento.
La implementación de Kaizen puede tener un impacto profundo en la cultura de una empresa al fomentar el trabajo en equipo, el empoderamiento de los empleados y una mentalidad de mejora continua. Al adoptar esta filosofía, las empresas están mejor posicionadas para maximizar su eficiencia y lograr resultados superiores a largo plazo.
Dónde puedo encontrar recursos y formación para implementar Kaizen y Lean Manufacturing
Implementar Kaizen y Lean Manufacturing en tu empresa puede ser un desafío, especialmente si no tienes experiencia previa en estos métodos. Afortunadamente, existen numerosos recursos y opciones de formación disponibles para ayudarte a adquirir los conocimientos necesarios y guiar tu implementación con éxito.
Aquí hay algunas fuentes donde puedes encontrar recursos y formación:
1. Libros y publicaciones
Una excelente manera de comenzar es investigar y leer libros sobre Kaizen y Lean Manufacturing escritos por expertos en el campo. Algunas recomendaciones incluyen "The Toyota Way" de Jeffrey Liker, "Lean Thinking" de James P. Womack y Daniel T. Jones, y "Gemba Kaizen" de Masaaki Imai. Estos libros te proporcionarán una comprensión profunda de los principios y prácticas clave.
2. Cursos en línea
Internet ofrece una amplia gama de cursos en línea que cubren aspectos específicos de Kaizen y Lean Manufacturing. Plataformas como Coursera, Udemy y LinkedIn Learning ofrecen cursos impartidos por profesionales de la industria que te permitirán aprender a tu propio ritmo y desde cualquier lugar. Busca cursos que se adapten a tus necesidades y asegúrate de leer las opiniones de otros alumnos antes de inscribirte.
3. Consultores especializados
Si prefieres recibir orientación personalizada, contratar a un consultor especializado en Kaizen y Lean Manufacturing puede ser una excelente opción. Los consultores pueden ayudarte a evaluar el estado actual de tu empresa, identificar áreas de mejora y diseñar un plan de implementación personalizado. Asegúrate de buscar consultores con experiencia demostrada y referencias sólidas para garantizar que obtengas el mejor servicio.
4. Grupos de estudio y redes profesionales
Otra forma efectiva de adquirir conocimientos y compartir experiencias es unirse a grupos de estudio o redes profesionales en el campo del Kaizen y Lean Manufacturing. Estos grupos te brindarán la oportunidad de conectarte con otras personas interesadas en estos métodos, intercambiar ideas y discutir desafíos comunes. Puedes encontrar grupos en plataformas en línea como LinkedIn o buscar asociaciones profesionales relacionadas con tu industria.
5. Eventos y conferencias
Asistir a eventos y conferencias relacionados con Kaizen y Lean Manufacturing también puede resultar beneficioso. Estos eventos suelen contar con ponentes expertos que comparten sus conocimientos y experiencias prácticas. Además, proporcionan una excelente oportunidad para establecer contactos con profesionales de ideas afines y aprender de las mejores prácticas implementadas por otras empresas.
Asegúrate de aprovechar al máximo los recursos disponibles y de adaptarlos a las necesidades específicas de tu empresa. La implementación exitosa de Kaizen y Lean Manufacturing requerirá tiempo, dedicación y compromiso, pero los beneficios en términos de eficiencia y gestión de procesos valdrán la pena.
Cuáles son algunos casos de éxito de empresas que han implementado Kaizen y Lean Manufacturing
La implementación de Kaizen y Lean Manufacturing ha demostrado ser altamente efectiva para mejorar la eficiencia y productividad en diversas empresas. A continuación, te presentamos algunos casos de éxito de compañías que han aplicado estos principios con resultados sobresalientes:
Toyota
Toyota es reconocida mundialmente por su excelencia operativa basada en los principios de Kaizen y Lean Manufacturing. La implementación de estas filosofías ha permitido a Toyota maximizar la calidad de sus productos, reducir los tiempos de producción y aumentar la satisfacción del cliente. Gracias a la mejora continua y la eliminación de desperdicios, Toyota se ha consolidado como una de las empresas más eficientes de la industria automotriz.
General Electric
Otro ejemplo destacado de éxito es General Electric, una empresa líder en el sector industrial. Mediante la adopción de Kaizen y Lean Manufacturing, GE ha logrado aumentar su rentabilidad, mejorar la calidad de sus procesos y reducir costos significativamente. El enfoque en la eliminación de desperdicios y la optimización de la cadena de suministro ha sido clave para el éxito de GE.
Zara
Zara, la famosa marca de moda española, también se ha beneficiado de la implementación de Kaizen y Lean Manufacturing. Esta empresa ha revolucionado la industria al adoptar un modelo de producción ágil y flexible. Mediante la reducción de tiempos de entrega, la optimización de inventarios y la mejora constante de sus procesos, Zara ha logrado mantenerse a la vanguardia de la moda y satisfacer las demandas cambiantes de sus clientes.
Estos son solo algunos ejemplos de cómo Kaizen y Lean Manufacturing han transformado positivamente diferentes industrias. La clave del éxito radica en la aplicación constante de estos principios, la involucración de todos los niveles de la empresa y el compromiso con la mejora continua.
Cómo puedo evaluar y medir los resultados de la implementación de Kaizen y Lean Manufacturing en mi empresa
Una vez que hayas implementado Kaizen y Lean Manufacturing en tu empresa, es fundamental evaluar y medir los resultados para determinar su impacto y eficacia. Aquí te mostramos algunas formas de evaluar y medir los resultados:
Análisis de indicadores de rendimiento clave (KPIs)
Los KPIs son herramientas importantes para evaluar el desempeño de cualquier proceso empresarial. Al implementar Kaizen y Lean Manufacturing, debes definir KPIs específicos que estén alineados con tus objetivos y que te ayuden a medir la eficiencia y productividad de tu empresa. Estos KPIs podrían incluir tiempos de ciclo, tasa de producción, calidad del producto, tiempo de entrega, entre otros.
Recopilación y análisis de datos
Es necesario recopilar datos relevantes durante y después de la implementación de Kaizen y Lean Manufacturing. Estos datos pueden incluir información sobre desperdicio de tiempo y recursos, problemas y retrasos en la producción, y cualquier otra métrica relevante. Utiliza estas métricas para analizar tendencias y identificar áreas de mejora potencial.
Encuestas y retroalimentación de los empleados
Los empleados son una fuente valiosa de información para evaluar y medir los resultados de la implementación de Kaizen y Lean Manufacturing. Realiza encuestas o entrevistas para recoger sus opiniones y experiencias sobre los cambios implementados. Su retroalimentación te ayudará a comprender mejor cómo ha afectado el cambio a su trabajo diario, y si han experimentado mejoras en términos de eficiencia y calidad.
Análisis de costos
Además de medir la eficiencia operativa, es importante analizar los costos antes y después de la implementación de Kaizen y Lean Manufacturing. Evalúa cómo han cambiado los costos de producción, de mano de obra y de desperdicio, y compáralos con los resultados obtenidos. Esto te permitirá evaluar si las mejoras realizadas tienen un impacto positivo en el desempeño financiero de tu empresa.
Comparación con estándares de la industria
Otra forma de evaluar y medir los resultados de la implementación de Kaizen y Lean Manufacturing es comparar el desempeño de tu empresa con los estándares de la industria. Investiga cuáles son los estándares aceptables en términos de eficiencia, productividad y calidad para empresas similares a la tuya. Si logras superar estos estándares, significa que tu implementación ha sido exitosa.
Seguimiento continuo
Una vez que hayas evaluado y medido los resultados iniciales de la implementación de Kaizen y Lean Manufacturing, no olvides realizar un seguimiento continuo. Esto te permitirá identificar si los beneficios obtenidos se mantienen a lo largo del tiempo y si es necesario realizar ajustes o mejoras adicionales.
Recuerda que la evaluación y medición de los resultados son procesos clave para asegurar que tu implementación de Kaizen y Lean Manufacturing sea efectiva y que continúe maximizando la eficiencia de tu empresa a largo plazo.
Cuáles son los desafíos comunes al implementar Kaizen y Lean Manufacturing y cómo superarlos
La implementación de Kaizen y Lean Manufacturing puede presentar desafíos comunes para las empresas que buscan maximizar su eficiencia. Sin embargo, estos desafíos pueden superarse con una planificación adecuada y el compromiso de todos los miembros del equipo.
Falta de comprensión y resistencia al cambio
Uno de los desafíos más comunes al implementar Kaizen y Lean Manufacturing es la falta de comprensión y la resistencia al cambio por parte de los empleados. Es importante educar a todo el personal sobre los beneficios de adoptar estas metodologías y cómo pueden mejorar la eficiencia y la productividad en general. Además, se deben proporcionar sesiones de capacitación para garantizar que todos comprendan los nuevos procesos y herramientas.
Falta de liderazgo y compromiso
Otro desafío común es la falta de liderazgo y compromiso por parte de la alta dirección. Para que la implementación sea exitosa, es crucial que los líderes se involucren activamente y muestren su compromiso con el cambio. Deben establecer metas claras, asignar recursos adecuados y liderar con el ejemplo al utilizar las prácticas de Kaizen y Lean Manufacturing en su propio trabajo diario.
Problemas de comunicación y colaboración
La falta de comunicación efectiva y colaboración entre los diferentes departamentos o equipos también puede dificultar la implementación de Kaizen y Lean Manufacturing. Es fundamental establecer canales de comunicación abiertos y fomentar un ambiente de colaboración en toda la organización. Esto puede incluir reuniones regulares de seguimiento, la creación de equipos multifuncionales y el uso de herramientas colaborativas.
Falta de seguimiento y evaluación continua
Una vez que se ha implementado Kaizen y Lean Manufacturing, otro desafío común es la falta de seguimiento y evaluación continua. Es esencial establecer indicadores clave de rendimiento (KPI) para medir el progreso y realizar ajustes cuando sea necesario. Esto implica recopilar datos, analizarlos y tomar acciones correctivas para mejorar aún más los procesos y resultados.
Implementación a gran escala
Otro desafío que puede surgir al implementar Kaizen y Lean Manufacturing es hacerlo a gran escala en una organización grande. En estos casos, es recomendable comenzar con un piloto o proyecto de prueba antes de implementar de manera completa en toda la empresa. Esto permite identificar y solucionar posibles problemas o ajustes necesarios antes de llevarlo a una escala más amplia.
Aunque la implementación de Kaizen y Lean Manufacturing puede presentar desafíos, estos pueden superarse con una planificación adecuada, liderazgo comprometido y una comunicación efectiva. Al abordar estos desafíos y seguir las mejores prácticas, las empresas pueden maximizar su eficiencia y lograr mejoras significativas en sus operaciones.
Kaizen es una filosofía japonesa que busca la mejora continua en todos los aspectos de una organización.
El objetivo del Lean Manufacturing es eliminar todo tipo de desperdicio y maximizar el valor para el cliente.
Algunas herramientas de Kaizen incluyen el análisis de flujo de valor, 5S, Poka-Yoke y Kanban.
Kaizen se centra en la mejora continua y en involucrar a todos los empleados, mientras que Lean Manufacturing se enfoca en la eliminación de desperdicios y la mejora de la eficiencia.
Los beneficios de implementar Kaizen y Lean Manufacturing incluyen reducción de costos, aumento de la calidad, mejora en los tiempos de entrega y mayor satisfacción del cliente.
Deja una respuesta
Entradas relacionadas